Fused cast refractories are manufactured by electro-fusing and casting process. Carefully selected high-purity raw materials are melted in Heroult type electric arc furnace at 1900 – 2500 ℃ and cooled to solidify after pouring into molds. Fused cast refractories have very high density and strength owing to electro-fusing process compared with ordinary types of refractories such as bonded refractories and stable mineralogical composition contribute to high resistance against corrosion and erosion by molten glass.
ZB-X950 Series ZB-X9510 ZB-X9540
AGC Ceramics has developed unique, first-class zirconia fused cast refractories by utilizing its years of accumulated fused cast refractories technology. ZB-X950 Series achieved highest level of quality without stone and blister defects in the molten glass. Therefore, it is suitable for the parts that come into contact with glass in fine glass melting furnaces. It has a proven performance in melting furnaces of boro-silicate glass, alumino silicate glass, glass ceramics and display glass.
ZB-X950 Series consists of ZB-X9510 for general use and ZB-X9540 with high electrical resistivity. The latter is suitable for electrode blocks that particularly need high electrical resistivity.
Chemical composition(%)
|
ZB-X9510 |
ZB-X9540 |
SiO2 |
4.0 |
9.3 |
Al2O3 |
0.8 |
1.5 |
ZrO2 |
94.5 |
88 |
Na2O |
0.4 |
0.02 |
Others |
0.3 |
1.2 |
The data (in this catalog) represents typical values and should not be considered as guaranteed specifications. These typical values can be varied without any notice.
Zirconite (ZB) Series
Zirconite series is high quality Al2O3-ZrO2-SiO2(AZS) fused cast refractories, consisting of crystallized baddeleyite (ZrO2) and corumdum (Al2O3), and matrix glass. The raw materials are carefully selected and fused in Heroult type electric arc furnaces.
Chemical composition(%)
|
ZB-1681 |
ZB-1681X |
ZB-1691 |
ZB-1691X |
ZB-1711 |
SiO2 |
13.5 |
10.5 |
12.0 |
12.5 |
12.0 |
Al2O3 |
52.0 |
55.3 |
50.8 |
50.0 |
45.8 |
ZrO2 |
33 |
33 |
35 |
36 |
41 |
Na2O |
1.3 |
1.0 |
1.9 |
1.4 |
1.0 |
Others |
0.2 |
0.2 |
0.3 |
0.2 |
0.2 |
The data (in this catalog) represents typical values and should not be considered as guaranteed specifications. These typical values can be varied without any notice.
Marsnite (MB) Series
Marsnite (MB) series are alumina fused cast refractories whereby highly pure alumina raw material is melted at over 2000°C and poured into a mold.
Chemical composition(%)
|
MB-G |
MB-C |
MB-U |
SiO2 |
0.8 |
0.8 |
0.2 |
Al2O3 |
95.0 |
96.5 |
93.0 |
Na2O |
3.5 |
2.0 |
6.5 |
Others |
0.7 |
0.7 |
0.3 |
The data (in this catalog) represents typical values and should not be considered as guaranteed specifications. These typical values can be varied without any notice.
Casting types
Fused cast refractories are manufactured by electro-fusing and casting process. After being poured molten material into molds, shrinkage voids occur in cooling and solidification process. The location of shrinkage voids is important for furnace design and is controlled by casting techniques as the following table.
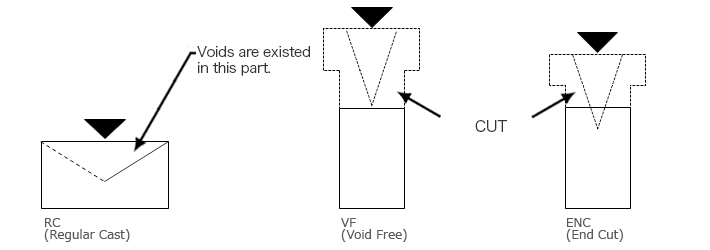
Casting types
Mark |
Casting type |
Remark |
RC |
Regular Cast |
The normal type of product including the shrinkage voids under the casting gate. |
VF |
Void Free |
The special type of product being removed the shrinkage voids after cooling. |
ENC |
End Cut |
For side wall blocks, most of the shrinkage voids are removed by the same method as VF. |
The products and casting types
|
ZB-X950 |
Zirconite(ZB) |
Marsnite(MB) |
|
ZB-X9510 |
ZB-X9540 |
ZB-1681 |
ZB-1681X |
ZB-1691 |
ZB-1691X |
ZB-1711 |
MB-C |
MB-G |
MB-U |
RC |
- |
- |
○ |
○ |
○ |
- |
- |
○ |
○ |
○ |
VF |
○ |
○ |
○ |
○ |
○ |
○ |
○ |
○ |
○ |
○ |
ENC |
- |
- |
○ |
- |
○ |
○ |
○ |
- |
- |
- |
Non-destructive Inspection Method
Fused cast refractories, which are used for important portions of glass furnaces should be guaranteed its inner structure.
AGC Ceramics Co., Ltd. is the first company in the world that has begun to inspect all AZS(Al2O3-ZrO2-SiO2) fused cast refractories in glass contact parts, such as side wall, throat, dam wall by non-destructive inspection method in 1994. We have accumulated our experiences more than 20 years and contributed to improve the reliability of glass melting furnaces and extend its life.